SPEE3D Collaborates With Northeastern University Kostas Research Institute
Purpose of collaborative effort is to bring additive manufacturing to students and military.

A WARPSPEE3D printer from SPEE3D was sold to Northeastern University and the school’s Kostas Research Institute (KRI) in Burlington, MA. Image courtesy of SPEE3D.
Latest News
January 31, 2025
SPEE3D, a metal additive manufacturing company, has sold a WARPSPEE3D printer to Northeastern University and the school's Kostas Research Institute (KRI) in Burlington, MA. The investment will teach students about cold spray additive manufacturing (CSAM) and allow the university to collaborate with the U.S. Army Research Laboratory (ARL) on materials development, quality control, and process control for large 3D prints.
The WarpSPEE3D is located at Northeastern University's Innovation Campus, a 70,000-sq.-ft. research and development facility. Northeastern University's Mechanical Engineering Department offers M.S. and Ph.D. programs, such as the Advanced and Intelligent Engineering M.S. program, which enables students to work intimately with AM platforms such as the SPEE3D printer for education and research. Northeastern University's Innovation Campus is also home to the Kostas Research Institute, which fosters links with the US Department of Defense, research agencies, and contractors.
“SPEE3D is excited to partner with Northeastern University's College of Engineering and the Kostas Research Institute, where faculty can work with students on our WarpSPEE3D printer and learn about Cold Spray Additive Manufacturing technology,” says Byron Kennedy, CEO at SPEE3D. “Additionally, the Institute's close ties with the military align well with our customer base. We look forward to a successful collaboration with the US Army Research Laboratory.”
“Northeastern University's Cold Spray Research Group is excited to have added SPEE3D's Cold Spray Additive Manufacturing technology with support from the US Army Research Laboratory,” says Dr. Ozan Cagatay, assistant professor of Mechanical and Industrial Engineering at Northeastern University “We will be leveraging their WarpSPEE3D printer for materials research and development, development of novel applications, and training future engineers, scientists, and skilled personnel. Our focus will be publishing high-quality research, addressing the needs of our stakeholders, and helping close the growing gap in the US advanced manufacturing workforce.”
SPEE3D's CSAM technology offers high-density metal parts at build rates up to 100 g/min (3.5 oz/min), accelerating prototyping and product development while minimizing operational downtime. The WarpSPEE3D printer can print parts up to 88 lbs. (40 kg) with a diameter of up to 40x30-in. (1m x .7 m) and is made for a research or factory environment.
Sources: Press materials received from the company and additional information gleaned from the company’s website.
Subscribe to our FREE magazine,
FREE email newsletters or both!Latest News
About the Author

DE’s editors contribute news and new product announcements to Digital Engineering.
Press releases may be sent to them via DE-Editors@digitaleng.news.
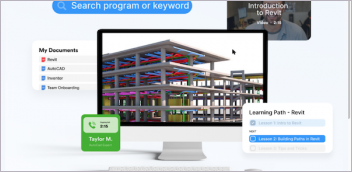
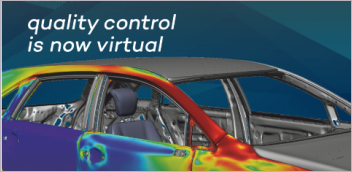
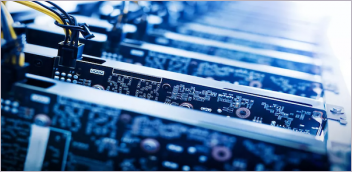
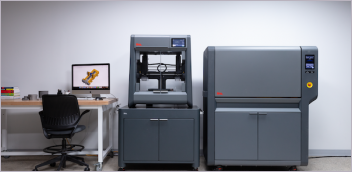