Festive FEA: Drop Testing a Candy Cane with Ansys LS-Dyna
In this guest post, the author, a consulting engineer from Rand Simulation, toys around with simulation of candy canes.

Brandon Finney of Rand Simulation simulates a candy cane for some holiday fun. Image courtesy of Brandon Finney, Rand Simulation.
December 30, 2024
By Brandon Finney
'Tis the season for festive engineering! This year, I decided to put my finite element analysis skills work on a seasonal icon: the candy cane. We all know the perils that follow once you see your beloved candy cane fall and shatter. With Ansys LS-Dyna, I set out to simulate what happens when a candy cane falls onto a rigid surface. Read on to see how I designed the experiment, developed a material model, and simulated the drop test—all while keeping things festive!
Building the Model
To capture the candy cane's iconic stripes into the model, I utilized mesh morphing. Although the candy cane's twisting introduced some skewing in the elements, we embraced the festive spirit and made the engineering assumption that this was acceptable.
I started this project with a candy cane plan, A sweet little profile to fit in my hand.
A cylinder came next, with a mesh oh so fine, To twist into something quite festive, divine.
Some profiles I made to help with the task, For morphing the mesh—it’s easy, just ask!
The stripes now appear in a classic design, They twist and they shimmer, a sight so fine.
With morphing complete, the mesh is just right, This candy cane’s ready—it’s quite the delight!
Material Definition
To understand the candy cane’s brittle behavior, I performed a simple 3-point bend test on a sample. The Sample broke around 50N of pressure. I did a quick bend test simulation in LS-Dyna to help determine the Young’s modulus and fracture stress to use in the drop simulation.
There are many material models available in LS-Dyna, and a quick search of material databases yielded no results for candy canes. So, to keep things simple I used *MAT_ELASTIC and *MAT_ADD_EROSION to add a sudden failure criterion since candy canes shouldn’t have much if any permanent deformation before failure. A more sophisticated material model could be built, but in the interest of having more time for family this holiday season we will keep it simple.
Candy Cane Bend Test 1
Candy Cane Bend Test 2
After the simulation we can output a force vs displacement curve to help validate our material model. You can see below my generated graph. Our simulation showed the break around 47N of force, which closely matches physical testing.

Drop Test Simulation
With the material model defined, I simulated the candy cane falling from a height of approximately 6 inches onto a rigid surface. To speed up the simulation time, I set an initial velocity of the candy cane just before impact. Key highlights of the drop test include:
Fracture Animation: The simulation showed the candy cane shattering into pieces, mimicking real-world behavior.
Visualization of the stresses during the impact event.
Once the model is built and running, it's easy to test additional load cases for different drop positions. For curiosity’s sake, I decided to see what would happen if it were dropped on the end instead of the side. The results are below.
Results and Insights
The drop test showed just how brittle candy canes are. While I’ve always known they were fragile, I was surprised to see it break into so many pieces from such a low height. It might be interesting to revisit this simulation with the plastic wrapping included to evaluate its effect on the results. Simulating the shipping packaging could also add an additional layer of complexity, but for now, let’s enjoy the festive chaos of our shattered candy cane this holiday season.
Brandon Finney is a consulting engineer at Rand Simulation, specializing in Mechanical FEA. He collaborates with customers to tackle complex engineering challenges and optimize product designs. Holding a Bachelors of Science in Mechanical Engineering Technology from Michigan Technological University, Brandon combines technical knowledge with hands-on experience. In the automotive industry, he refined designs by leveraging simulation for virtual validation in steering column crash applications. His expertise in LS-DYNA enables him to deliver innovative solutions across diverse industries.at Rand Simulation.
More Ansys Coverage
Subscribe to our FREE magazine,
FREE email newsletters or both!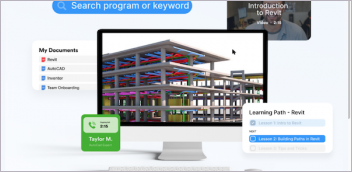
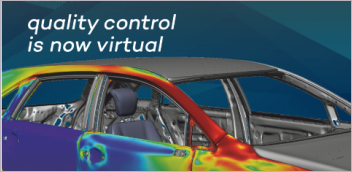
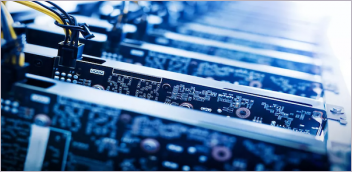
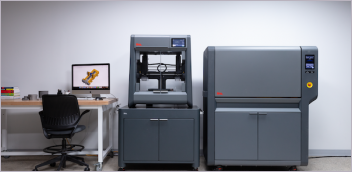